Eco-design and composite materials: major movement or an underlying trend?
If flax fibre can help reduce the environmental impact of a composite material, the eco-design of a product accentuates the approach to sustainability. From the plant to development of materials, the production process, the circular economy, and the end of life of composites.
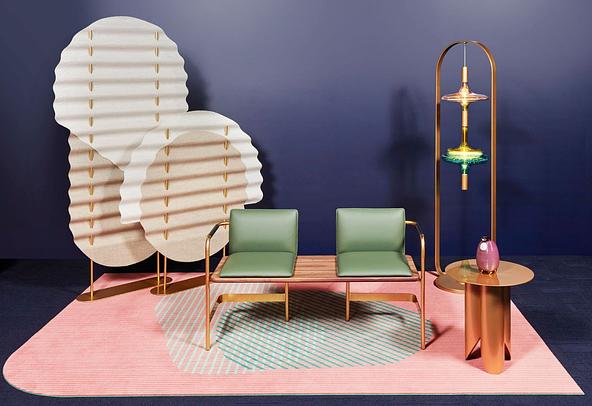